Pola & Massa: PeM 650-DS Planarising
Double Sided Grinding machine removing excess plugging paste
The PeM Planarizer machine is an evolution of the single side Pola e Massa Planarizer machine mod. 650 for deburring and cleaning without oval deformation of holes and has been successfully sold in the market for more than 20 years. Specifically designed for applications as VIA HOLE PASTE REMOVAL, SURFACE TREATMENT and DEBURRING OF SHARP CORNERS, HOLE EDGES AND IRREGULAR PERIMETERS, it has been recently implemented to be more performing, especially in term of treating thin material and double side treatment but also to selectively work on a specific zone of the PCB’s.Pola e Massa consolidate experiences has allowed to build the double side PeM Planarizer with all the necessary technical devices required to obtain a perfectly flat surface on the whole board.
Wet processing brushing machine for:
- Via hole paste removal
- metal surface treatment
- deburring of sharp corners, hole edges and irregular perimeters
Main features:
- Vertical axis rotating and oscillating brushes
- No hole oval deformation
- Control by PLC complete with touch screen
- Adjustable brush pressure
- Automatic zero set-point procedure
- Variable brush speed
- Adjustable belt conveyor speed
- Independent brushes management (speed and pressure)
- Suitable to treat thin material
- Different brush grit combinations are possible to control copper surface roughness
- Easy and fast maintenance
- Double sided treatment
Advantages:
Less piece manipulation; critical especially for thin material,
- Single brush adjustment in term of abrasion power-pressure and speed,
- Easier and faster automatic locking -unlocking system for all brushes,
- Possibility to replace each single brush,
- Different position of the first row of brushes and the second row for each side of treatment (alternating movement)
- Lower production costs for a full brushes kit replacement,
- Easier and faster replacement of the transport belt,
- Possibility to switch off/on each brush,
- Easier and faster maintenance,
- Brushless motors for a better efficiency,
- Motorized transport rollers, rubber covered,
- Piece treatment down to 0,1 mm (plus CU) thickness
- Better piece uniformity,
- New gear/sensor (encoder) at entry measuring panel width; value used to adjust inside the machine brushes oscillation. Better precision in measuring,
- Dedicated rollers to avoid warping during the process,
- New software with brushes able to lift them up when moving laterally on the panel edges and down when moving towards the centre of the panel.
- More performing double ring diamond brushes; different grits available.
- Different type of brushes with different grit available for a wide range of applications.
- Copper removal in cleaning epoxy approx. 2-3 µm each pass depending of panels features, selected brushes and selected parameters.
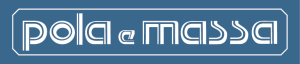