Plasma Technology
Plasma Etching:
Plasma etching is the removal of material from surfaces through plasma processes. It is also called dry etching because conventional etching processes are carried out with wet chemical methods using corrosive acids. The plasmas of the process gases change the aggregate state of the material to be etched from solid to gaseous phase, and the vacuum pump extracts the gaseous products. Masks can be used to etch partial areas or structures only. Plasma etching is only carried out in low-pressure plasma because:
- A longer treatment duration is necessary to achieve the desired etching effects;
- Also, most etching gases can only be used in low-pressure plasma.
Plasma etching is suitable for a wide range of applications. To tailor the etching process optimally to the application, a variety of process gases are available, and one of the following three basic etching processes can be used.
ION Etching
Depending on the application, it is also called “physical etching”, “sputtering” or “micro sandblasting”.
Argon or other noble gases which form ions but no radicals are used as processes gases. The etching effect is realized by knocking out atoms or molecules from the substrate by the kinetic energy of the electrons accelerated in the electric field.
Applications:
-
Micro-structuring of surfaces e.g. for adhesion improvement (“micro sandblasting”)
-
Bombarding of a vapor deposition source (“sputtering”)
As ion etching does not have a chemical effect, it works on almost every substrate (practically non-selective). The etching effect of the plasma acts almost exclusively in the acceleration direction of the ions. The effect is highly anisotropic.
Chemical Plasma Etching:
The molecules of process gases used are mostly broken down into radicals in the plasma. The etching effect is mainly based on the reaction of these radicals with the atoms or molecules of the substrate and their conversion to gaseous degradation products.
Primary Applications:
- Decomposition of oxide layers;
- Removal of photoresist (“stripping”);
- Ashing of matrices for analysis;
- Etching of PTFE;
- Structuring and microstructuring of semiconductors
Plasma etching is highly selective, i.e., process gases and substrates must be perfectly matched. The etching effect is isotropic, i.e. has the same effect on all sides.
Reactive Ion Etching:
In the plasma, gas molecules form radicals and positively charged ions. For etching, the reactive effect of the radicals as well as the kinetic energy of the ions can be used, if the plasma excitation occurs by accelerating the ions in the electric field and using them to bombard the substrate.
Reactive ion etching combines the effects of ion etching and plasma etching: There is a certain anisotropy, and materials which do not react chemically with the radicals are etched. Most importantly, the etching rate is considerably increased. By bombardment with ions, the substrate molecules are put into an excited state which makes them much more reactive.
Applications:
- Primarily in semiconductor etching
PTFE Etching:
Plasma technology can provide adhesiveness to plastics which are normally “non-glueable” due to their low surface energy. With polypropylene (PP), polyethylene (PE) or polyoxymethylene (POM), this is achieved by activation in the oxygen plasma. For PTFE, the plastic material with the smallest surface energy, the activation process is not sufficient to achieve the desired result. The fluorocarbon bonds cannot be broken in oxygen plasma.
In hydrogen plasma, however, hydrogen radicals combine with the fluorine atoms of PTFE and thus break the carbon bonds. When hydrogen fluoride gas is extracted, unsaturated carbon compounds remain, to which polar liquid molecules can easily attach.
A brownish discoloration on the PTFE surface shows that etching has taken place.
Activation:
Good wettability is a prerequisite for the adhesion of a surface with the bonding partner in the painting, gluing, printing or bonding. Wetting is not only impaired by contamination with oil and grease; many materials have surfaces which, even if clean, cannot be sufficiently wetted by many liquids such as adhesives and paints. The liquid rolls off. It will not adhere to the surface even after curing or drying.
The reason is that the surface energy of the substrate is low. Materials with lower surface energy can wet materials with higher surface energy, but not vice versa. Therefore, the surface energy of the applied liquid, also known as surface tension in the case of liquids, must be lower than that of the substrate.
The surface energy of most plastics is too low to be wetted by adhesives and coatings. This is due to their non-polar surfaces. No attachment site is available for the applied liquids.
In plasma activation, the surface is activated by increasing surface energy. In this process, attachment sites are created for the applied liquid.
Conventional activation uses chemical primers as liquid adhesion promoters, which are highly corrosive and harmful to the environment. On the one hand, they require adequate evaporation time before further processing; on the other hand, their activated state cannot remain too long. Also, non-polar materials such as polyolefins cannot be sufficiently activated by chemical primers
In addition, activation can be carried out in arch or corona discharge. This is a form of atmospheric pressure plasma treatment. However, it can only treat flat or convex surfaces, which are introduced into the arc during such treatment.The arced plasma is blown out through a nozzle. This allows the activation of component surfaces with complex curvature.
During activation in an air or oxygen plasma, the non-polar hydrogen bonds of plastic polymers are replaced by oxygen bonds which provides free valence electrons for bonding with liquid molecules.
Plasma activation at low or atmospheric pressure provides the surfaces of “non-glueable” plastics such as POM, PE and PP with excellent adhesiveness and sprayability. It offers accurate adjustment options for the desired surface energy; this can prevent over-activation, which can result in undesired surface etching.
In low-pressure plasma, other gases besides air and oxygen can also be used, which can, in place of oxygen, accumulate nitrogen (N2), amines (NHx) or carboxyl groups (-COOH) as reactive groups.
The activated state of plastics can last from several weeks to several months. However, it is advisable to carry out follow-up processing as soon as possible, as a cleaned surface will still attract dust, organic contamination and while in storage.
Plasma treatment can also give PTFE adhesiveness. However, this is not achieved through activation but by etching.
Generally, the surface energy of metals, ceramics and glass is higher than that of plastics. Nevertheless, there are also applications where these materials benefit from plasma activation. The surface tension of solder alloys is likewise high, so they roll off many metal surfaces. Therefore, plasma activation of metals can be used to improve wetting during soldering. It should be noted that the activation of metals is mostly effective only in a few minutes, and (inline) soldering must be carried out immediately after activation.
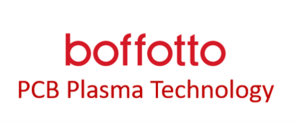